Un pool di scienziati del Consiglio Nazionale delle Ricerche CNR ISASI &IPCB (Sara Coppola, Veronica Vespini, Gennaro Gentile e Pietro Ferraro) ha messo a punto un metodo originale per “confezionare” dei liquidi con una membrana sottilissima di polimero biocompatibile e biodegradaile. Che si presta a molteplici sviluppi per packaging sostenibili, economici e originali. Ecco il paper pubblicato sulla rivista Science Advances.
“Confinare” l’acqua grazie ad una pellicola sottilissima e biodegradabile è un modo attraente per creare un vero e proprio packaging che consente di controllare la “forma dell’acqua”. L’acqua è una delle sostanze più importanti sulla Terra per la nostra vita, ricopre due terzi della superficie terrestre ed è un mezzo essenziale per i microrganismi viventi e per molti processi tecnologici e industriali.
Una tendenza crescente nell’industria dell’imballaggio, data la maggiore consapevolezza dell’importanza della sostenibilità dei processi, è quella di avere prodotti biocompatibili e biodegradabili. Disporre di contenitori che abbiano queste caratteristiche e che facilmente si possano adattare al contenuto, non essendo necessariamente più rigidi, rappresenterebbe un importante passo in avanti, soprattutto in termini di innovazione. Questo articolo si propone di illustrare i progressi significativi compiuti nel mondo del packaging, grazie ad un nuovo metodo che permette di rivestire con un sottile film di polimero volumi di acqua o materiali a base acquosa, i quali rimangono così racchiusi e sigillati all’interno di uno strato di polimero. Un modo per creare un vero e proprio packaging intorno a sistemi acquosi, rivestendo completamente i liquidi anche quando assumono forme complesse e transitorie. Potremmo definirlo un packaging a impatto ridotto e sempre più sostenibile, grazie a un processo innovativo che rispetta l’ambiente.
Cosa si intende per packaging veloce?
La possibilità di isolare, ingegnerizzare e modellare materiali in forme bidimensionali o tridimensionali complesse tramite tecniche di ingegneria bottom-up, su scala sia micro che macro-metrica, sta acquisendo crescente importanza nella scienza dei materiali. A oggi, i tecnici utilizzano una varietà di metodi complessi e costosi per la micro-fabbricazione, tra cui ad esempio la polimerizzazione a due fotoni, la litografia a interferenza, il replica molding e processi multistep per modellare e plasmare il materiale polimerico di interesse. Tuttavia, la maggior parte dei protocolli richiede dei pre-trattamenti chimici e fisici per ottenere le proprietà finali desiderate. Tali trattamenti oltre ad essere invasivi rispetto al risultato finale, sono anche onerosi da un punto di vista di costo e di tempo. Il metodo proposto è, invece, un processo molto veloce che permette di ottenere una pellicola sottilissima in grado di rivestire volumi di acqua o materiali gelatinosi 3D a base acquosa, e può essere attivato ogni qual volta ci si trovi in presenza di una superficie rivestita d’acqua. Il processo avviene istantaneamente e in modo completamente spontaneo, a partire da una piccola goccia di soluzione polimerica. Il polimero impiegato nello studio è l’acido poli(lattico- co-glicolico), PLGA. Il PLGA è un polimero biodegradabile e biocompatibile, che per il processo di packaging dell’acqua o degli idrogeli viene disciolto in dimetilcarbonato (DMC) a una concentrazione specifica. Il DMC è un solvente organico che dissolve facilmente il PLGA ed evapora lentamente. Quando la soluzione polimerica (PLGA/DMC) entra in contatto con una sostanza ad alto contenuto d’acqua (o con una stessa goccia d’acqua), un film di PLGA si forma istantaneamente attorno a essa, adattandosi alla geometria del sistema acquoso, che funge da guida.

Quando la soluzione entra in contatto con l’acqua, il solvente viene estratto ed è la variazione della tensione superficiale a guidare la formazione istantanea del film che si espande in modo conforme alla geometria assunta dal liquido. Il processo avviene in qualche secondo e, grazie alla lenta estrazione del solvente, si genera un film omogeneo e non poroso. Controllando la quantità di polimero impiegata è possibile controllare lo spessore del rivestimento prodotto, mentre controllando la forma assunta dal liquido è possibile modellare il corrispondente rivestimento polimerico.
Packaging sulla superficie dell’acqua
Da quanto spiegato nel precedente paragrafo, quando una goccia di una soluzione polimerica di PLGA disciolto in DMC viene posta su una superficie d’acqua, istantaneamente si osserva la formazione di un film continuo non poroso. Con un approccio di tipo bottom–up , siamo così in grado di rivestire una superficie d’acqua grazie all’autoassemblaggio (self-assembling) del polimero. Questo processo è caratterizzato da una versatilità senza precedenti, capace di consentire la formazione di membrane in grado di avvolgere liquidi o ambienti ricchi di acqua in diverse geometrie. Il PLGA attualmente è ampiamente utilizzato nel settore biomedicale ed è parte di molti dispositivi terapeutici, approvati dalla Food and Drug Administration (FDA), grazie alla sua biodegradabilità e biocompatibilità. Il processo di packaging avviene sia nel caso di una goccia appoggiata su una superficie, sia nel caso di una goccia pendente da un orifizio o di un film liquido depositato all’interno di un contenitore: in quest’ultimo caso il polimero può rivestire e sigillare tutta la superficie libera del pelo dell’acqua. Possono essere rivestiti completamente anche volumi di gel o in generale di materiale altamente idratato e di una qualsiasi forma. Il metodo di packaging proposto è funzione del volume utilizzato ma, dipende anche dalle proprietà della soluzione polimerica (materiali scelti, viscosità, concentrazione). Per la caratterizzazione delle membrane prodotte sono stati utilizzati una varietà di metodi, tra cui, ad esempio, la microscopia a scansione elettronica (SEM), prove di permeabilità e caratterizzazioni delle proprietà meccaniche quali la misurazione del modulo di Young. Le immagini SEM acquisite hanno rivelato una struttura polimerica simmetrica non porosa e caratterizzata da una superficie e uno spessore omogenei.
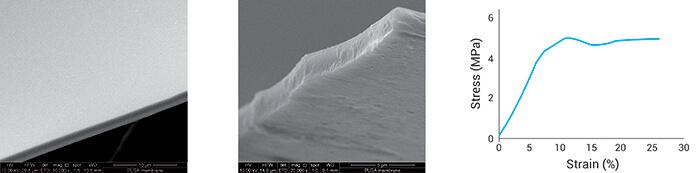
In particolare, utilizzando un SEM (Quanta FEG 200, FEI, Eindhoven, The Netherlands) in modalità di vuoto spinto, si è osservata la superfice e la sezione di una membrana. Prima delle osservazioni SEM i campioni di membrane sono stati montati su dei supporti opportuni e sono stati ricoperti con uno strato sottilissimo di metallo (Au- Pd con spessore compreso tra 5 ed 10 nm ). Tutti i campioni sono stati osservati con una tensione di accelerazione di circa 20 kV utilizzando un rilevatore secondario di elettroni. Per la misura dello spettro UV-visibile della membrana polimerica è stato utilizzato uno spettrofotometro (V-570 Jasco, Easton, PA, USA) che opera nella porzione di spettro compreso tra 200 e 800 nm di lunghezza d’onda e con una risoluzione di circa 0.5 nm. La membrana ha mostrato una buona trasparenza alla luce visibile con una trasmittanza superiore al 90% per le lunghezze d’onda investigate. I test meccanici sono stati effettuati su campioni di dimensioni rettangolari di spessore di circa 1.5 micron, larghezza 6 mm e lunghezza 10 mm utilizzando uno stage a controllo remoto ed alta precisione. Tali campioni sono stati posizionati su un dispositivo di test (Deben, Woolpit, UK) per registrare le curve di tensione e deformazione a circa 25° ± 1 °C con un’umidità relativa del 50 ± 5%, un carico di circa 200 N e una velocità di deformazione di circa 0.1 mm/min. Un esempio di curva di deformazione ottenuta dalle misure condotte sui campioni di PLGA è riportata nell’immagine sovrastante.
Il modulo di Young registrato per la membrana è di circa 75 ± 1 MPa, con un valore di punto di snervamento di circa 5.3 ± 0.2 MPa. I valori rilevati sono consistenti con i dati riportati in letteratura per i film di PLGA, tenuto conto delle diverse geometrie del campione e delle condizioni di test. Più in particolare, il modulo di Young ottenuto per le membrane risulta inferiore al valore riportato in letteratura a causa della minore velocità di deformazione utilizzata nel nostro dispositivo di test. Per quanto riguarda le misure di permeabilità e le proprietà di barriera è stato impiegato un campione di film circolare di circa di 2 cmq (Multiperm apparatus ExtraSolution, Pisa, Italy), nelle stesse condizioni di temperatura e umidità delle prove precedenti. La permeabilità è stata valutata per l’ossigeno e il vapore acqueo; per quest’ultimo è stata rilevata una buona proprietà di barriera. I valori registrati pari a 140 ± 8 (g μm)/(mq day kPa) sono, infatti, più di un ordine di grandezza inferiori rispetto a quelli riportati in letteratura per il PLA, mentre la membrana ha mostrato un’elevata permeabilità all’ossigeno, parametro molto importante in caso di applicazioni biomediche. Il valore di permeabilità all’ossigeno è di circa 1.90 × 105 ± 0.12 × 105 (cm3 μm)/(mq day atm) e risulta circa un ordine di grandezza più alto di quello del PLA. Per queste caratterizzazioni sono state utilizzate delle membrane realizzate sul pelo libero della superfice acquosa in un contenitore del tipo piastra di Petri. Lo spessore medio delle pellicole realizzate con questo metodo, e a valle delle caratterizzazioni effettuate, risulta dell’ordine di pochi micrometri. Le membrane prodotte sono trasparenti e presentano un modulo elastico di circa 75 MPa. Infine, sono state effettuate misure sull’angolo di contatto delle membrane si nota un valore medio di 73° ± 1°, tipico di polimeri leggermente idrofilici. In confronto con i film convenzionali di acido polilattico (PLA), l’angolo di contatto per l’acqua risulta più basso a causa delle presenza di minori segmenti idrofobici di acido glicolico rispetto a quelli di acido lattico. Ulteriori ricerche sono in corso, variando la concentrazione del polimero nella soluzione di DMC e la coppia polimero/solvente per modulare lo spessore e le proprietà del film. I materiali utilizzati nel processo sono i seguenti: il PLGA 50:50 (38,000 to 54,000 Da; PLGA Resomer RG 504H, Boeringer Ingelheim) è stato disciolto in DMC [20 to 30 (w/v); DMC, 99%; Sigma-Aldrich) al 25% in peso.
Il processo di formazione della membrana in caso di materiali gelatinosi a base acquosa è semplice e veloce. La soluzione di polimero/solvente viene colorata con l’aggiunta di un fluoroforo per garantire un migliore contrasto durante l’acquisizione delle immagini. Quando la soluzione entra in contatto con la superficie libera della struttura gelatinosa, la membrana si forma istantaneamente, adeguandosi alla forma e ai bordi della struttura utilizzata come guida. Come visibile in Figura 3 la superficie triangolare appare trasparente prima della formazione della membrana e colorata al termine del processo. Per dimostrare la presenza del sottile film di polimero, si utilizza un supporto di teflon per recuperare la membrana triangolare.
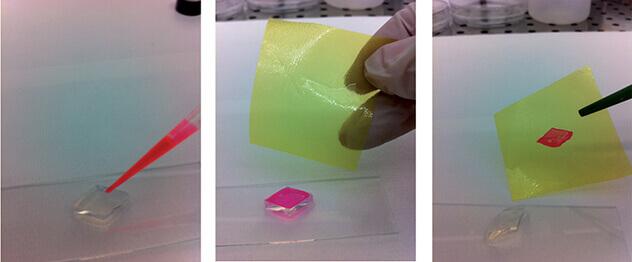
Il processo di packaging può essere impiegato anche in caso di strutture più complesse, come accade per una matrice di sfere immerse in acqua. Infatti, seguendo lo stesso processo di formazione, le sfere sono completamente rivestite da un sottilissimo film polimerico che si adatta alla struttura e alla superficie sottostante. In Figura 4 i riflessi della luce consentono di visualizzare il packaging trasparente e supportato dalle sfere, anche al termine del processo di evaporazione del liquido in cui erano immerse.
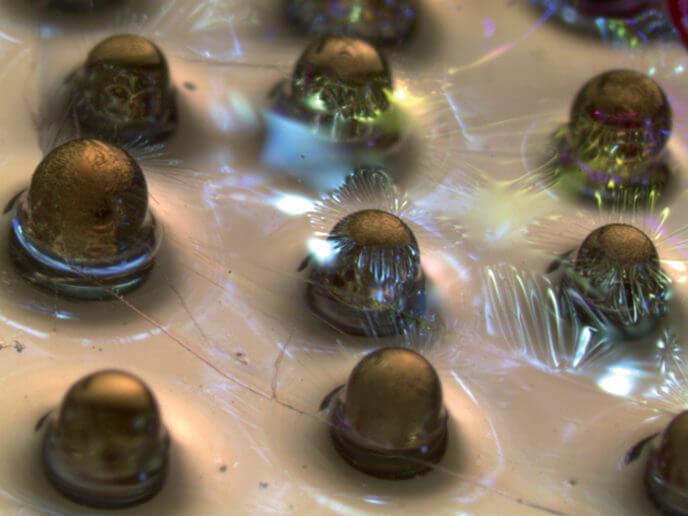
Conclusioni
Il metodo proposto rappresenta un nuovo approccio ingegneristico del tipo cosiddetto bottom–up, ecologico ed economico che consente la formazione istantanea di un packaging polimerico in presenza d’acqua. Il metodo proposto apre a molteplici possibilità di utilizzo e applicazioni, a partire dal settore biomedicale fino a coinvolgere processi industriali e di trasformazione, essendo utile per il trasporto, la preservazione e la protezione da agenti esterni. Inoltre, esperimenti di biotecnologia in microgravità, scienza dei materiali e lo studio della fluidodinamica possono sfruttare la possibilità di creare dei contenitori di acqua biocompatibili, biodegradabili e facilmente modellabili. Ulteriori sperimentazioni e dimostrazioni dei risultati ottenuti su scala macroscopica possono allargare il campo di applicazione verso approcci di natura industriale e automatizzata.