Per raggiungere nuovi livelli di flessibilità nella produzione e stampa di packaging, Bobst ripensa i processi di spalmatura e finissaggio e inventa Multi-Stack Unit: un’unità “bivalente” flexo-roto, che permette di attivare in pochi minuti la tecnologia desiderata, con grandissime economie e massima semplicità.
La necessità
Quando si parla di ibridazione fra tecnologie nel narrow web, di solito ci si riferisce a una combinazione di flexo e roto, offset, digitale per gestire con flessibilità dati variabili, nobilitazioni e finitura. Se invece parliamo di fascia media e larga il discorso cambia e l’attenzione va anche alla spalmatura. Il mercato domanda packaging sempre più sofisticati, che richiedono l’integrazione della macchina da stampa con gruppi in grado di realizzare innumerevoli tipologie di nobilitazione, coating, funzionali, personalizzazione… e anche di assicurare ai nuovi materiali sostenibili che la R&D crea con ritmo incalzante le barriere necessarie a garantire la shelf life dei prodotti. Ma…
“Ma”, al contempo, il converter ha bisogno di semplicità e di costi sostenibili, mentre le sue linee tendono a diventare sempre più complesse e costose, rallentate e difficili da gestire – e sappiamo quanto disporre di un’impiantistica “user friendly” oggi sia più importante che mai.
La sfida
Comporre tutte queste esigenze, per certi versi contrastanti, in una macchina unica, ben funzionante e sostenibile, per i progettisti rappresenta una bella sfida. Bobst l’ha raccolta e ha sviluppato una soluzione semplice e essenziale come l’uovo di Colombo.
Mettendo a fattor comune il know-how dei Competence Center di San Giorgio Monferrato (roto, accoppiamento e spalmatura) e Bielefeld (flexo di fascia media e larga), e prendendo il meglio della tecnologia storica del gruppo, il costruttore svizzero ha lavorato a realizzare un’unità “multi-stack” che integra i due processi flexo e roto. Da attivare in pochi minuti a seconda delle necessità, per poter effettuare, su qualsiasi tipo di substrato plastico e cellulosico, i diversi tipi di finitura e trasformazione: colori di stampa addizionali, verniciatura, coating, cold sealing….
La soluzione
Si chiama Multi-Stack Unit ed è pensata per poter lavorare in linea integrata a valle di una flexo a tamburo centrale – o una roto o altro ancora – con un investimento incommensurabilmente più basso rispetto all’acquisto di due stazioni distinte. Facile da gestire e con il passaggio da una tecnologia all’altra in pochissimi minuti, lavora su un’unica piattaforma con un processo ottimizzato, anche sul piano della sostenibilità: la Multi-Stack Unit occupa uno spazio limitato, il singolo passaggio in linea richiede meno energia rispetto alla somma di gruppi specializzati in linea o stand-alone, e gode dell’efficienza della tecnologia di asciugamento Bobst. Ce la descrivono Sara Alexander, responsabile marketing e comunicazione per le linee di stampa roto, accoppiamento e spalmatura presso la Bobst Italia di San Giorgio Monferrato, e Marco Carrara, Technology Sales Director delle CI Flexo per il printing e converting, di stanza a Bielefeld (D).
Appena nata, tutti la vogliono
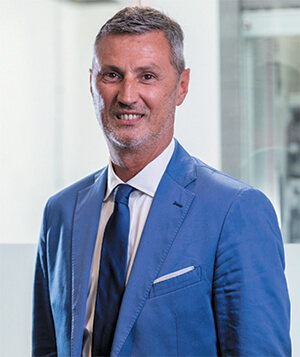
Marco Carrara
«Oggi per fare una spalmatura roto su una macchina flexo bisogna comperare un’unità apposita e integrarla in linea, e altrettanto dicasi per le spalmature flexo per cui bisogna dotarsi di unità aggiuntive. Gli investimenti sono altissimi e le linee diventano sempre più grandi e complicate da gestire. Bisognava affrontare il problema: gli utilizzatori ce lo chiedevano espressamente: prima un cliente tedesco, poi un grande gruppo austriaco…», esordisce Marco Carrara. Che aggiunge un’altra considerazione stimolante: «la R&D di nuovi substrati sostenibili corre, con caratteristiche inedite e sempre nuove esigenze di spalmature e vernici barriera, e per i converter è difficile prevedere di cosa avranno bisogno già domani.
Attrezzarsi con un’unità dove poter fare tutti i tipi di spalmatura per poter rispondere a esigenze sempre più varie e mutevoli è ormai essenziale per presidiare il mercato e la fortuna della Multi-Stack Unit ne è la riprova: abbiamo realizzato le prime due per rispondere a richieste specifiche ma poi abbiamo visto che questa soluzione interessava tantissimo, e l’abbiamo industrializzata per la produzione in serie. Prima ancora di presentarla ufficialmente al mercato ne avevamo già vendute quattro e ormai le potenzialità di sviluppo commerciale sono evidenti: la Multi-Stack Unit risponde a una necessità diffusa».
All’origine dell’idea
«Potendo unire il know-how di San Giorgio e di Bielefeld lo sviluppo è stato relativamente veloce», racconta Marco Carrara. «Abbiamo iniziato a lavorarci l’estate scorsa partendo dalla semplice richiesta di un gruppo flexo per spalmature. Ma poi il cliente ha iniziato a ricevere delle richieste di cold seal, che poteva eseguire solo acquistando un gruppo roto ad hoc oppure lavorando fuori linea su un’accoppiatrice… L‘idea di realizzare un’unità in grado di gestire entrambe le tecnologie flexo e roto è nata da qui».
«La nostra unità multipla ha risolto il problema alla radice: partendo da tecnologie ben collaudate e con un investimento ridotto, quel converter si è dotato di uno strumento che gli permette di effettuare su tutti i materiali, dal polietilene alla carta, tutti i tipi possibili di lavorazione. E di affrontare così, con una flessibilità estrema, gli sviluppi di una domanda in piena fase di sperimentazione, che prende mille rivoli e ha ancora poche certezze», sottolinea Alexander.
Un gioco astuto di cilindri, e non solo
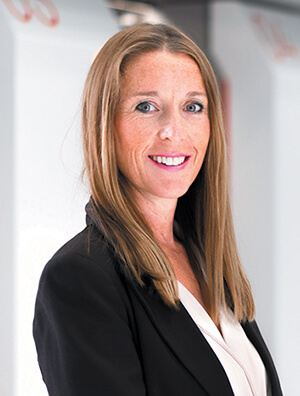
Sara Alexander
Il cuore e il senso stesso della Multi-Stack Unit di Bobst risiede nel cambio rapido di tecnologia «perché, ovviamente, se per spostarsi da flexo a roto occorresse fermare la macchina per delle ore, il vantaggio si ridurrebbe di molto». Sulla Multi-Stack Unit questo passaggio si effettua in soli 6 minuti, coadiuvato da avviamenti velocissimi, un sistema di inchiostrazione autopulente molto avanzato, messa a registro automatica e un sistema di essiccazione avanzato, che mantengono la qualità del lavoro elevata lungo l’intera tiratura. Ma il segreto – il famoso uovo di Colombo – risiede nel gioco di rulli che vengono gestiti in modo da poter lavorare, alternativamente, come elementi flexo o roto.
«Nella nostra unità Multi-Stack – dice Carrara – il cilindro di stampa e il rullo pressore della roto possono cambiare di posto e assumere la funzione del cilindro portacliché e dell’anilox flessografici e, anche se bisogna sostituire la camera a racla, nel complesso il passaggio è semplice e rapidissimo. Il risultato è una flessibilità mai raggiunta con il minimo di interruzioni e con la garanzia di un comando e controllo dei parametri automatico e senza complicanze, gestita dal supervisore dell’unità stessa».
La Multi-Stack Unit raggiunge facilmente velocità operative di 600 m/min in linea con le macchine da stampa flexo Bobst, che diventano 800 m/min a seconda dei lavori, ed è disponibile con larghezze di 1250, 1560 e 2150 mm in flexo e 1250 mm in roto. A completamento di una macchina possono essere installate fino a 4 unità multi-stack, senza compromettere le performance del sistema.
Il mercato chiede soluzioni multifunzione
«All’inizio pensavamo di svilupparla e proporla solo per le configurazioni di più alta gamma delle macchine rotocalco e flexo a tamburo centrale, ma poi ci siamo ravveduti: la Multi-Stack Unit porta valore a prescindere. Infatti adeguando, per esempio, il design ai diversi modelli di flexo CI ne abbiamo da poco vendute 4, due per il modello MASTER CI e due per il modello VISION CI, confermandone quindi la validità per converter di qualsiasi dimensione». Sara Alexander e Marco Carrara sono d’accordo. Non si tratta solo di sfruttare tutte le opportunità di business aperte da una soluzione innovativa e inedita – Bobst è la prima a proporre questo tipo di tecnologia – ma anche di guardare più in là dell’occasione contingente, per vedere come si sviluppa il mercato.
Un mercato, considerano i due manager, costituito in larga parte dal packaging alimentare, un mondo immenso che spazia dagli snack al fresco passando per il pet food, e che già da qualche anno chiede macchine che facciano più della sola stampa. «Per poter servire le richieste sempre più sofisticate dei brand owner – spiega Alexander – ma anche per il vorticoso sviluppo di materiali alternativi più sostenibili per tutte le applicazioni di imballaggio flessibile. Le esigenze di coating cambiano di conseguenza, rendendo difficile prevedere per quale tecnologia di spalmatura optare. Meglio attrezzarsi per poter fare tutto!».
E la sostenibilità? Ambientale, economica e culturale
La Multi-Stack Unit di Bobst nasce da un’esigenza operativa e economica, ma non per questo i benefici in termini di sostenibilità sono poco significativi. «Occupare poco spazio, sprecare meno materiale in fase di start up perché lavoriamo su una sola un’unità, consumare meno energia, risparmiare tempo… tutto rende la Multi-Stack Unit sostenibile per natura, con il corollario di saving economici tutt’altro che marginali», sottolinea Carrara. E poi – ripete Alexander – permette di lavorare con i nuovi materiali sostenibili che tutti si stanno impegnando a sviluppare, e innesca una cultura della collaborazione che oggi è vitale: «Il fatto che Bobst possa mettere i campo tutte le tecnologie rappresenta un incredibile vantaggio, soprattutto perché oggi mondi lontani si stanno avvicinando, come quelli della metallizzazione e della stampa, ad esempio.
I clienti chiedono soluzioni, fanno domande e per essere preparati dobbiamo saperli ascoltare e integrare il più possibile le competenze, dei partner di filiera e nostre interne. Superando anche le barriere geografiche e di “tifoseria”: ed è fantastico vedere i team dei vari centri tecnologici considerare i colleghi con interesse e con orgoglio, consapevoli dell’eccellenza delle rispettive competenze e delle potenzialità enormi della collaborazione».