Solid new features from Uteco, global leader in printing and converting plants, who presented at K the Rainbow 4.0 laminating machine and the Total Green solventless technology, developed in collaboration with Sun Chemical and Sapici. And for drupa it announces…
Excellent redemption of Uteco at K 2019 where, compared to the previous edition, the Veneto group registered an increase in attendance and (active) market interest for its entire production range – flexo, gravure, digital and laminating presses – from both emerging countries and by economies that have long been cautious. This is undoubtedly due to the economic situation that focuses the attention of consumers and legislators on the processing and converting of plastics and, backwards from that, onto the packaging chain. But, as Aldo Peretti, President and CEO of the group claims, it is «Uteco’s ability to propose, investing constant resources and involving the most active consumable and substrate manufacturers, that creates innovation. In this way, we rightfully take on the leading role, on a technical, economic and ethical level, in developing the sustainability the world so badly needs. And thus showing what the converting chain is worth, where the elements that transform packaging from mere containers into precious tools for the conservation and communication of consumer goods are created and produced. And that also increasingly make the difference in terms of environmental compatibility». At the German plastics fair, Uteco presented a live demo of the new, compact and high-performance Rainbow 4.0 laminating machine as well as the state of the art of solventless lamination.
Entry level 4.0
To meet the widespread need for a machine capable of handling most flexible films, with particular attention to different tensions, after 8 months of prototyping and testing, in 2016 the Rainbow 4.0 machine was created. It has been designed with Industry 4.0 criteria and a particular attention to reduction in energy consumption. This machine presents some unique technological solutions that are leading edge compared to those offered by other market leaders. The production speed is one of its main features: it reaches 500 m/min, placing itself among the highest in the entry level category.
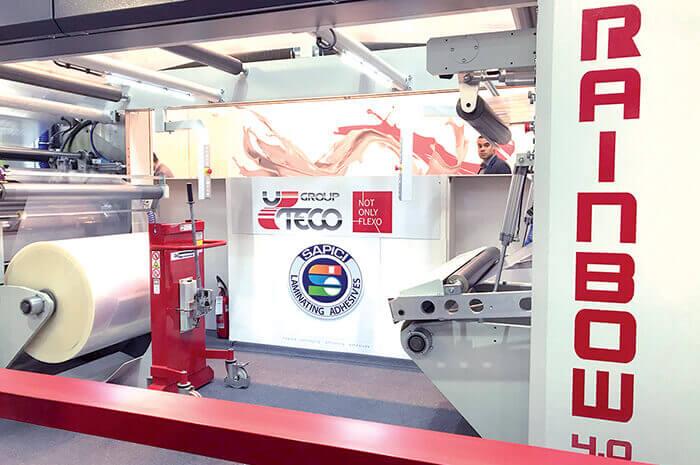
The sleeve factor
Rainbow 4.0 is equipped with an automatic sleeve removal system which allows for quick job changes and optimal cleaning of the same. The machine adopts a type of elastomer sleeve ideal for coating with solvent-free, bi-component glues. The basic polymer, with the anti-adhesive components added, prevents the external surface cells from clogging during operations and maintains ideal surface tension values; this facilitates the coating, while also reducing glue consumption compared to traditional coatings. This sleeve, which was used for demos throughout the entire period of the fair, has a surface hardness of 80 Shore A, a pressure resistance of 25 Kg/cm and works at a maximum temperature of 140°C.
Hi-tech application and washing
Rainbow 4.0 is equipped with a new infrared technology developed by Synaptik, for the uniform application of minimum quantities of adhesive over the entire surface of the material. The system continuously monitors the transfer of the adhesive onto the coated material, alerts the operator if the reading results are incorrect and records the grams per square meter of adhesive poured, allowing the entire lamination process to be controlled. Another feather in Uteco’s cap provided in the basic configuration of the Rainbow 4.0 is the automatic washing system for cleaning all rollers. Through special spray nozzles integrated in the machine, the detergent (solvent free and therefore non-toxic and non-flammable) eliminates all traces of adhesive at the end of the lamination process.
Substrates and consumables, a crucial factor
In order to achieve a film fully recyclable in the industrial sector, materials supplied by Jindal film have been used. The first unwinder featured the use of Bicor 40MB344US, a transparent 40 µm multilayer BOPP with Ultra Seal technology, which provides an improved seal compared to traditional OPP for hot welding. This material offers high a high welding and puncture resistance, good adhesive grip and avoids the need to use a PE sealing film while working only with PP-based materials.
The second unwinder featured the 16 µm Alox-lyte 16AO894 a biaxially oriented, transparent, high barrier PP that is vacuum coated on one side with aluminium oxide. This is in fact a transparent solution that is an alternative to other barrier films such as, typically, metallic films, aluminium foil and PET films coated with AlOx or SiOx, which, like same, enables the extension of the food shelf life. Rainbow 4.0 thus produces a 2-layer PP barrier material, i.e. a sealable laminate that constitutes an excellent monomaterial solution, in line with recycling requirements.
The inks supplied by SunChemical are also consistent and relevant to this project. The SOLIPROP V series used are suitable for printing on a considerable number of substrates and for lamination with adhesives. They offer excellent printability, suitable for printing on various polyolefin films, good thermal resistance at 170-180 °C, a scratch resistance on external prints and a good degree of gloss.
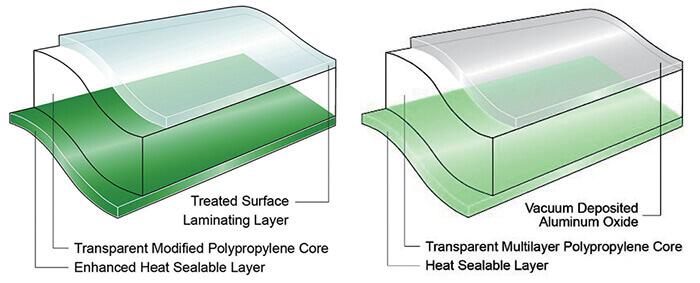
A new adhesive from the Sapici-Uteco partnership
Sapici presents Polurflex 7910/6051, a product born out of the collaboration between Sapici and Uteco, a perfect synergy between the experience in polyurethane chemistry and the state of the art of bonding and lamination machines. A technology Made in Italy which implements a demonomerization process thus ensuring the absence of free monomers. The adhesives obtained are solventless with a free di-isocyanate threshold of less than 0.1%, and with undetectable (already immediately after the lamination) PAA) and NIAS levels in line with the European chemical agency opinion (ECHA/NA/17/29) concerning restrictions on the use of di-isocyanates. Furthermore, there are no dangerous substances such as cyclic esters, NPG, Bisphenol A etc. that can migrate to the food, neither before nor after the thermal processes. Another important feature: the extreme stability degradation during recycling processes opens up new and appealing scenarios for the recovery of the material and its reuse. Normally, solvent-based products on the market require the use of a common symbols that list any characteristics that might provide a danger to human health. Sapici’s product though does not require any GHS (globally harmonized system) or MSDS (material safety data sheet) risk phrases, as it is free of substances hazardous to human health and the working environment.
Test data
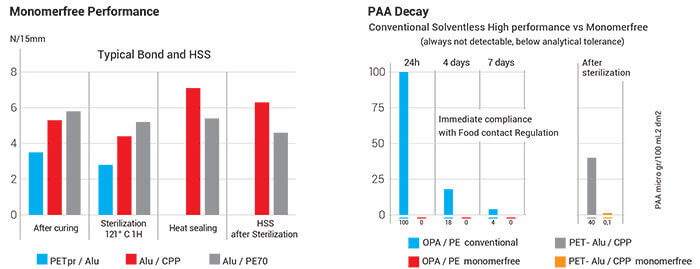
The histograms features the results of comparative stress tests on a 15 mm specimen. The first two columns show the adhesion force between three different laminated materials after the completion of the crosslinking and, subsequently, after sterilization at 121 °C; the second two show the adhesion force after welding and of the weld after sterilization. As for the decay of aromatic amines, the table below shows the comparison between traditional SL (solvent less) adhesives and Sapici’s SL Monomer free version during the crosslinking times and after food sterilization. Here it should be underlined how the product packaging end user, when treating the laminate with sterilization or pasteurization processes, has the assurance that the aromatic amines do not form anew via the breakage of the internal bonds of the polyurethane, thanks to the absence of the free monomer. The product laminated with Rainbow 4.0, thanks to the fast crosslinking process, enables the converter to lower production times, cutting the storage costs of the materials: it hence allows the material to be produced and the packaging to take place after a few hours, without waiting for the long and expensive crosslinking and decay times of the Primary Aromatic Amines. The laminate provides barrier properties to aromas, gases and moisture. It also avoids any risk phase due to the presence of isocyanates (characteristic of any conventional adhesive on the market) and is perfectly in line with all food packaging and workplace safety regulations (also potential future ones). This not only confirms both Sapici and Uteco’s commitment to the innovative value of the projects developed together, and to the return on investment and competitiveness, but also to operator safety and the healthiness of the workplace.