Tempi di avviamento, produzione oraria, fermi improduttivi. Sono i tre parametri su cui è costruito il nuovo pacchetto di strumenti e procedure messo a punto in Saica Flex in collaborazione con i partner tecnologici per raggiungere nuovi livelli di efficienza in flessografia.
Si chiama Flexo175 per via della lineatura di stampa raggiunta, ed è stato perfezionato in6 anni di R&D condotta con apertura mentale, amore per la tecnologia, precisione. Nemico giurato dell’approssimazione, per parlare del progetto Flexo175 Luca Salatin (Responsabile Prestampa e innovazione tecnologica per la stampa flessografica in Saica Flex Italia) parte dai dati rilevati direttamente dal sistema di raccolta a bordo macchina di ogni linea di produzione, assumendo la stampa rotocalco a benchmark di qualità. Documentano gli straordinari traguardi del nuovo metodo di stampa flessografica di Saica Flex Italia, che si traducono concretamente in risparmio di energia, economie di gestione, minore impatto sull’ambiente. E con una qualità dei lavori che rende complicato distinguere quale delle due tecniche sia stata effettivamente utilizzata.
«Abbiamo iniziato questo progetto con la consapevolezza che in flessografia ci fosse ancora molto da mettere a punto – afferma Salatin – ma i risultati conseguiti hanno superato le nostre stesse aspettative: se i saving ottenuti con Flexo175 sono tali da fare la differenza sul mercato, lo è ancora di più l’aver raggiunto lo standard di stampa a 70 linee /cm ovvero i 175 lpi che danno nome al progetto. E anche se il mercato non sempre richiede un tale livello di eccellenza, questo traguardo ci consente di oltrepassare la realtà tecnologica attuale, con una visione di prospettiva chiara per il futuro. Ma andiamo con ordine.»
Lei afferma che “Sostenibile non è solo cosa produci, ma anche come lo produci”. Cosa intende?
Oggi le opportunità di crescita si basano non solo sulla capacità di offrire prodotti sostenibili – laminati monomateriale, packaging compostabili e tante altre soluzioni eco-sostenibili giustamente apprezzate – ma anche sul saper mettere in campo processi realmente circolari. Dove, cioè, le risorse vengono gestite con efficienza e senza sprechi, si distingue fra vero e falso “green”, si sa valutare se un processo all’acqua sia più “puro” di uno a solvente…
Si tratta di leve competitive fattuali e per questo stimate: l’approccio alla sostenibilità che non si esprime tramite processi concreti è superato e oggi gli operatori, anche grazie alla disponibilità di strumenti sempre più avanzati, iniziano a verificare le informazioni e a fare i conti. Chi sarà in grado di interpretare e mettere a terra per primo questi strumenti godrà sicuramente di un vantaggio rilevante nei prossimi anni.
Quand’è iniziato il lavoro che ha portato a Flexo175?
Quando Saica ha investito in macchine da stampa di ultima generazione (due flexo e una roto, NdR) su cui aveva senso testare nuove ipotesi e nuovi tools. Da quel momento è iniziato il nostro percorso: sperimentare e costruire quel rapporto di fiducia e collaborazione con fornitori – selezionati secondo criteri specifici e partendo dalla loro propensione all’innovazione – che oggi permette a noi di provare in anteprima nuove tecnologie e a loro di ottenere i feedback utili alla messa a punto finale di un nuovo prodotto tecnologico.
Le variabili in gioco nella stampa flessografica, si sa, sono molte e ciascun converter mette a punto la propria “ricetta”… qui a Meldola lavoriamo sul nostro standard senza fermarci mai, vista la rapidità con cui evolve questa tecnica di stampa. E stiamo già mettendo le basi del prossimo step, in vista di un’evoluzione ulteriore del nostro pacchetto di strumenti e dei relativi risultati.
Che risultati concreti avete ottenuto?
Le nostre macchine da stampa sono impostate con specifiche analoghe in modo che tutti i tools siano perfettamente compatibili, in funzione di un lavoro che ha per obiettivo la standardizzazione estrema. Grazie all’utilizzo e al confronto dei dati di produzione tra le due tecnologie è possibile capire e interpretare le differenze e seguire
le tendenze di miglioramento. Tempo medio di avviamento inferiore, incremento della produttività oraria e miglioramento della percentuale dei fermi improduttivi, sono solo i dati più significativi emersi sulle nostre macchine Flexo nel 2024.
Insomma, che la roto sia più veloce e più adatta alle tirature lunghe non è sempre così vero…
Diciamo che la nostra esperienza ci consente di affrontare tirature corte, medie e long run con la certezza e la consapevolezza di arrivare a performance spesso sorprendenti nei confronti della rotocalco. Con Flexo175 abbiamo abbattuto il tabù psicologico delle 70 linee per cm, quindi anche il livello di qualità di stampa ora è perfettamente paragonabile.
Avete considerato il costo di utilizzo dei diversi impianti?
Un elemento importante, ma non l’unico, per affrontare il tema dei costi di utilizzo è certamente il consumo energetico. Comparando le due tecnologie abbiamo raccolto numerosi dati nel corso del tempo e su questo aspetto la flexo risulta – positivamente – a ridotto consumo. L’obiettivo può essere sicuramente molto più ambizioso tenendo conto del potenziale sviluppo da parte dei costruttori in ottica 5.0
In questo lavoro di R&D che ruolo hanno avuto i fornitori?
Fondamentale. Li selezioniamo con estrema cura, dopo ricerche e verifiche e scegliamo quelli con le tecnologie migliori, all’avanguardia, capaci di utilizzarle al meglio… che non si fermano mai e guardano al futuro con il nostro stesso approccio. Con Inci.Flex, ad esempio, abbiamo costruito nel tempo un rapporto costante di scambio e aggiornamento sulle nuove opportunità che offre la tecnologia.
Il Crystal Quarz che Enzo Consalvo ha presentato durante lo scorso OH a Fisciano, noi abbiamo iniziato a interpretarlo e testarlo circa un anno e mezzo prima e con reciproco beneficio: Inci.Flex ha potuto mettere a punto lo sviluppo delle lastre contando sul nostro contributo tecnico e in Saica Flex abbiamo “assaggiato e scoperto” in anteprima assoluta un nuovo sistema di incisione che ha contribuito direttamente ai risultati di Flexo175.
In che modo?
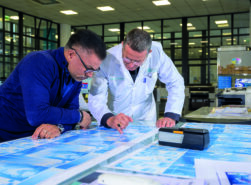
Enzo Consalvo e Loreto Simoncelli, Inci.flex
Già a inizio 2023, in concomitanza con i primi test monocromatici effettuati sul Crystal Quartz, ne abbiamo intuito il potenziale e abbiamo iniziato a lavorare insieme con l’obiettivo di portare la stampa flessografica a un livello nuovo. Da subito l’espressione qualitativa della lastra incisa in Crystal Quartz ha evidenziato una minore necessità di inchiostrazione a fronte di una stesura dell’inchiostro impeccabile e densità dei pieni percentualmente superiori alle tecnologie precedenti. Questo ha poi consentito importanti sviluppi anche nell’aumento della frequenza dei retini.
Il bello di lavorare con Enzo Consalvo è che siamo entrambi appassionati di tecnologia e ne parliamo, facciamo esperimenti, proviamo nuovi materiali, tipi di incisione, retini…
Con il suo responsabile dell’area flexo, Loreto Simoncelli, abbiamo lavorato addirittura sulle tempistiche di produzione e adeguato il tipo di incisione alle nostre macchine…
E per quanto riguarda gli altri elementi del pacchetto stampa?
Li abbiamo completamente rivisitati tutti. Per restare sui fotopolimeri, abbiamo scelto di sviluppare equamente con i nostri principali partner le tecnologie Esko e Kodak e parallelamente, sempre in collaborazione con realtà dinamiche e votate all’innovazione, ci siamo fortemente impegnati nello sviluppo di nuove mescole di elastomeri.
Per la parte anilox, dal 2020 abbiamo fatto una scelta radicale e investito sulla tecnologia a carburo di tungsteno, un materiale molto duro e dalla rugosità estremamente bassa, che ci ha consentito di migliorare non solo la qualità di stampa ma anche la riduzione dei fermi improduttivi e di conseguire un risparmio di inchiostro che con Flexo175 in quadricromia arriva fino a un 20%.
Un ruolo altrettanto importante è stato giocato dai nostri fornitori di inchiostri e di biadesivi, che hanno sposato il nostro approccio e ci hanno sempre proposto prodotti particolarmente innovativi, così come accade per la parte più meccanica del processo, dove abbiamo trovato nuove soluzioni tecnologiche sul pacchetto sleeve e carrier.
È tutto merito delle macchine e dei nuovi componenti oppure il personale dà un contributo rilevante?
Essenziale. Una delle cose più preziose ottenute con questa lunga sperimentazione è stata proprio l’innalzamento delle competenze di tutti gli elementi dell’intero reparto di stampa.
All’inizio, francamente, abbiamo dovuto affrontare la fatica di rompere abitudini, scardinare pregiudizi, trovare le motivazioni per il maggiore impegno richiesto da nuovi modi di lavorare. Ma oggi i miei collaboratori e tutti i colleghi in reparto sono i primi a cercare nuove sfide, perché hanno verificato che organizzazione e standardizzazione si traducono concretamente in coinvolgimento e soddisfazione per tutti.