From the last World Manufacturing Forum 2019 in Cernobbio, information, experiences, reflections on the concrete scope of the industrial revolution 4.0. Under the lens, the product-service and the new role of homo faber in manufacturing that creates value by processing data. An editorial by Andrea Briganti, Director of Acimga and Federazione Carta e Grafica, to open the mind.
A year after the first time I took part in the World Manufacturing Forum in Cernobbio, of which I gave a full rendition to our readers, albeit belatedly beyond a timely chronicle of events, I would like to share with you some further considerations regarding the contents of this important annual event and hence regarding the second time I attended.
Last year much was said of Industry 4.0 and IoT, or how, from data, technologies today allow us to understand what and how to produce and customize and likewise allow us achieve a production paradigm that does not necessarily lead to the production of batches in series, but is capable of creating data, which becomes information and which allows extreme customization and even predictive maintenance, changing not only the concept of production, but also that of service.
The manufacture that produces services
This latter dynamic is perhaps still little analysed and correlated, but from my point of view the modification of the production possibilities not only impacts the value chain, revolutionizing its consequentialities and therefore its timing, it also overwhelmingly affects the concept of service. The needs of the consumer or B2B customer are no longer responded to by the mere offering of a physical product, but thanks to an application of paradigm 4.0, a new service is provided in response to the customer’s industrial or personal needs, this both in industrial as well as physical terms.
Hence Industry 4.0 is not only an element of efficiency and efficacy as I was referring to in my article last year, but I believe it is above all an element of servitisation, intended as a response to a service expected by the customer through the production of an article.
My meaning of servitisation probably does not exactly correspond to the definition given in the Garzanti dictionary: (econ.) process whereby a product is no longer offered or sold alone, but supplied in combination with a service.
In my opinion, in fact, the personalized and predictive production of products or remote assistance and continuous learning deriving from the data and information that the company’s consumption and production creates, translated into manufacturing, are themselves a service.
Hence my provocation is to assert that, seen from a manufacturing perspective, Industry 4.0 is itself a service when it manifests itself in a product or process aimed at creating a product specially tailored to the needs of the individual customer.
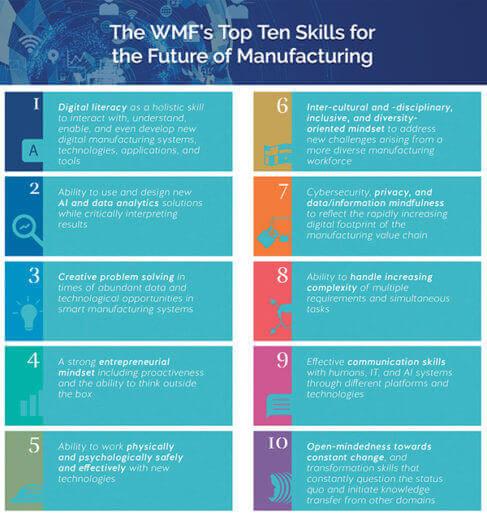
A point of no return
In any case, the fourth industrial revolution offers us the opportunity to create a mix of products and services or servitised products, unique in the history of the great industrial revolutions.
Like all revolutions it implies a point of no return and this we must postulate both as operators of the industrial system, as well as in our role as managers and entrepreneurs. We can no longer side-step the computerization of the production process, neither the processing of systemic and clustered data of our customers; this no longer with a view to correlating the technical characteristics of standard products with SWOT analysis on the target, but the product-service itself becomes the enactment of the wishes of that particular cluster, be this industrial or the final consumer.
Hence, in a world that shies away from returning to the integration between analogical and digital, between off-line and on-line, in this second article we all take the application of paradigm 4.0 for granted.
Human resources
The problem faced by the WMF in this second “thematic” edition is the human factor.
The revolution, once the theoretical and strategic phase is over, enters the concrete implementation phase with a vision that soon becomes a “hygienic factor”, that is, a factor for which the customer does not expect a failed implementation but an indispensable system of offers.
To do this you need skills, new business functions, new organizational charts and matrixes in which to insert digital skills, with the difficulties of cultural matches between new professional skills and production functions based on traditional skills related to research and development, design, production seriality, catalogued production offers.
All this while facing the challenge of making the workplace appealing for new figures and stimulating those who must reposition themselves within the company.
So basically it is no longer a technological fact, but a fact that impacts on human resources, on the organization chart and skills, both new and old.
A new organizational ecosystem
Therefore, a false myth must be debunked, that the industrial revolution 4.0 will replace people with machines or computers. On the contrary, it will offer new job opportunities, new cultural contaminations and skills that will also increase the company and product vision. Hence B2B will not necessarily be characterized by performance and technical specifications, but can also feature in areas and for declinations and characteristics previously hardly thinkable in terms of technological offer alone.
From here, considerable and multiple future organizational scenarios can be assumed: the development of ecosystems of companies integrated with each other but based on modular assets according to customer clusters, regions, production cultures or simple demands for volume.
The figures of system integrators who increasingly possess information that becomes production specifications will be able to interpenetrate cultural or social paradigms translating them into productive value chains. A further step in the paradigm development curve.
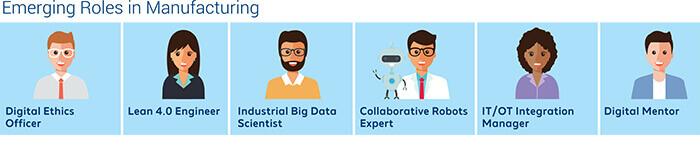
Skilled humanism with cross competences
Hence one has the figure of man with different skills who will become even more central, or that is that CPU and that ability capable of giving an overall sense to the product, data, information and able to integrate systems at the engineering design level of production networks and ecosystems.
We can therefore see the centrality of man on two axes: that of the ability to give data an interpretation and therefore to derive information useful for productive and predictive manufacturing, as well as the ability to integrate systems and value chain procedures that are increasingly network- and less consequential flow based.
Paradoxically man is even more at the center, but a man who is well prepared, possessing digital but above all cross-sectorial skills, where the interpretation of the data is multidisciplinary, multicultural and not merely technical and technological.
Supply chain training: a path for the companies
Precisely by virtue of these considerations, ACIMGA and the Paper and Graphics Federations, as well as the Italian Government itself with the Stability Law, have taken steps to try to give operators in the supply chain new operational skills, through a path started in 2018 and which is ideally divided into three phases.
A first step saw the check-up, corresponding to the first phase inserted in the Stability law for technological supply with the institution of hyper amortization, then a second phase in the classroom in SDA Bocconi and a third phase with a one-by-one auditing and check-up with Enzo Baglieri and his collaborators from the Product and Process Innovation Department of the Bocconi University Business Management School. All this to culturally train entrepreneurs and to give the first company lines cultural and approach tools.
And now?
Industry 4.0 is no longer a strategic choice but a company need to enable competition on a global and national level.
Summing up, Industry 4.0 is based on the integration between the world of analogical (off-line) manufacturing and the world of digital as a data processing tool which, under careful HUMAN direction, becomes information capable of making processes more efficient but also (and above all) to servitise the products, in the sense that the manufactured product becomes itself a service for its target, even going beyond the concept of product-service mix.
This will create new ways of productive ecosystems, not necessarily linked to the consequential flow model of the value chain but modular and dynamic. All this thanks to renewed organizations and with skills that differ from the 3.0 model. With man ever more – and this is the great paradox – at the centre, with his value that stands apart from the seriality of the machine and of thought.
An interpretative, multicultural, social and, why not, emotional thought. The new manufacturing man on the horizon. A beautiful challenge, primarily cultural and human.