Start-up times, production rates, unproductive downtimes. These are the three parameters for the new package of tools and procedures developed at Saica Flex in collaboration with technology partners to achieve new levels of efficiency in flexography.
It is called Flexo175 because of the print line achieved, and has been perfected over 6 years of R&D conducted with open-mindedness, love of technology, and precision. Interview with Luca Salatin, Head of Prepress and Technological Innovation for Flexo Printing. Sworn enemy of approximation, to talk about the Flexo175 project Luca Salatin starts from the data collected directly from the on-board collection system of each production line, taking rotogravure printing as a quality benchmark. They document the extraordinary achievements of Saica Flex Italia’s new flexo printing method, which translate concretely into energy savings, management economies, less impact on the environment. And with a print quality that makes it complicated to distinguish which of the two techniques was actually used.
«We started this project with the awareness that there was still a lot to be fine-tuned in flexography,’ says Salatin, ’but the results achieved have exceeded our own expectations: if the savings achieved with Flexo175 are such as to make a difference on the market, it is even more so to have achieved the 70 line/cm printing standard, or the 175 LPI that gives the project its name. And even if the market doesnot always demand such a level of excellence, this achievement allows us to go beyond the current technological reality, with a clear vision for the future. But let’s go in order.»
You state that ‘Sustainable is not only what you produce, but also how you produce it’. What do you mean by that?
Today, opportunities for growth are based not only on the ability to offer sustainable products – singlematerial laminates, compostable packaging and many other eco-sustainable solutions that are rightly appreciated – but also on knowing how to implement truly circular processes. In other words, where resources are managed efficiently and without waste, where a distinction is made between true and false ‘green’, where it is possible to evaluate whether a water-based process is more ‘pure’ than a solventbased one…
These are factual competitive levers and are therefore valued: the approach to sustainability that is not expressed through concrete processes is outdated and today’s operators, thanks also to the availability of increasingly advanced tools, are beginning to verify informations and do the maths. Whoever is able to interpret and ground these instruments first will certainly enjoy a major advantage in the coming years.
When did you start the work that led to Flexo175?
When Saica invested in the latest generation of printing machines (two flexo and one roto, EdN) on which it made sense to test new hypotheses and new tools. From that moment, our journey began: experimenting and building that relationship of trust and collaboration with suppliers – selected according to specific criteria and based on their propensity for innovation – which today allows us to preview new technologies and enables them to obtain feedback useful for the final fine-tuning of a new technological product. As we know, there are many variables at play in flexographic printing, and each converter develops its own ‘recipe’… here in Meldola we work on our standard without ever stopping, given the speed with which this printing technique evolves. And we are already laying the foundations for the next step, with a view to further evolving our toolbox and results.
What concrete results have you achieved?
Our printing machines are set up with similar specifications so that all tools are perfectly compatible, with the aim of extreme standardisation. By using and comparing production data between the two technologies, it is possible to understand and interpret the differences and follow trends for improvement. A lower average start-up time, an increase in hourly productivity and an improvement in the percentage of unproductive downtimes recorded on flexo machines in 2024 are the most significant data I will only quote.
In short, that roto is faster and better suited for long runs is not always so true…
Let’s say that our experience allows us to tackle short, medium and long runs with the certainty and knowledge that we can achieve often astonishingperformance compared to gravure. With Flexo175 we have broken the psychological taboo of 70 lines per cm, so even the level of print quality is now perfectly comparable.
Have you considered the cost of using the different systems?
An important element, but not the only one, to address the issue of usage costs is certainly energy consumption. By comparing the two technologies we have collected a lot of data over time and on this aspect flexo is – positively – low in consumption. The goal can certainly be much more ambitious taking into account the potential development brought on by manufacturers in a 5.0 perspective.
In this R&D work, what role have suppliers played?
Fundamental. We select them with extreme care, after thorough research and verification, and choose the ones who offer the best cutting-edge technologies, who are able to use them to the fullest… are unstoppable and look to the future with our same approach.
With Inci.Flex, for example, we have built over time a relationship of exchange and constant updating on the new opportunities offered by technology. We began working with and testing the Crystal Quartz about one year and a half before it was unveiled by Enzo Consalvo during the last OH in Fisciano, with mutual benefit: Inci.Flex was able to fine-tune the development of the plates relying on our technical contribution while, here in Saica Flex, we had the opportunity to be the absolute first to preview the new engraving system that directly contributed to the results of Flexo175.
How?
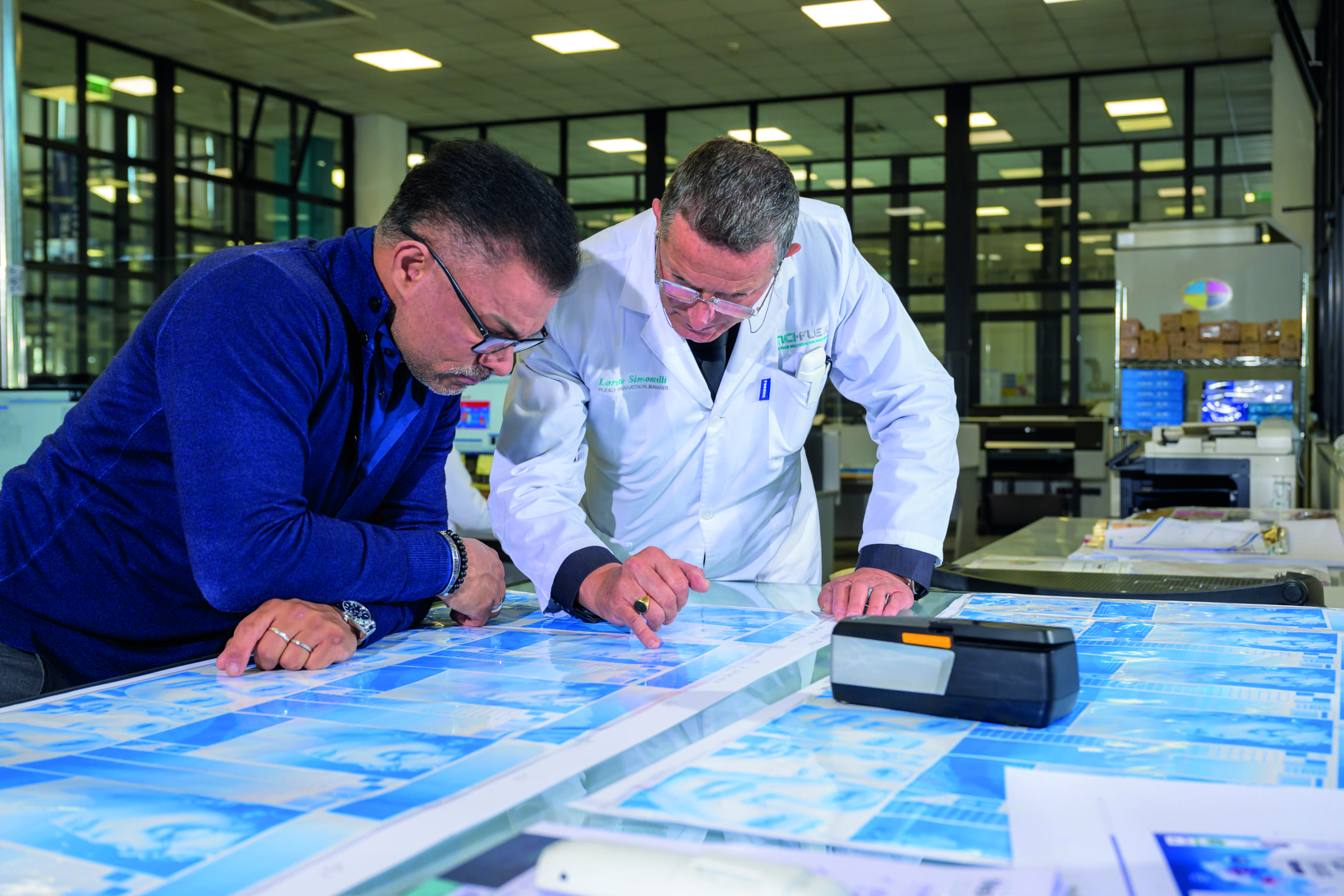
ENZO CONSALVO, LORETO SIMONCELLI, Inci.flex
Already at the beginning of 2023, in conjunction with the first monochrome tests carried out on the Crystal Quartz, we realised its potential and began working together with the aim of taking flexographic printing to a new level. From the outset, the qualitative expression of the Crystal Quartz engraved plates showed a lower ink requirement in the face of an impeccable application and a higher percentage of full-colour density than previous technologies. This has also allowed important developments in the increase in screens frequency. The great thing about working with Enzo Consalvo is that we are both passionate about technology: we talk about it, we do experiments, we try new materials, types of engraving, screens… With their flexo area director, Loreto Simoncelli, we even worked on production times and adapted the type of engraving to our machines…
And what about the other elements of the printing bundle?
We’ve completely revisited them all. To remain on the subject of photopolymers, we have chosen to develop Esko and Kodak technologies equally with our main partners and at the same time, in collaboration with dynamic and innovation-driven companies, we have strongly committed ourselves to the development of new elastomer compounds. For what concerns anilox, instead, in 2020 we made a radical choice to invest in tungsten carbide technology, a very hard material with extremely low roughness, which has allowed us not only to improve the quality of the print but also the to obtain a significant reduction of down-times and to achieve, with Flexo175 in four-colour, up to 20% in ink saving.
An equally important role has been played by our inks and double-sided adhesives suppliers, who have embraced our approach and have always proposed particularly innovative products to us, as is the case for the most mechanical part of the process, where we have found new technological solutions for the sleeve and carrier division.
Are these resuts strictky rekated to the new machines and components or do the staff make a significant difference?
Simple. One of the most valuable things we obtained with this long experimentation was precisely the improvement of the skills of all the individuals in the entire printing department.
At the beginning, frankly, we had to face the struggle of breaking habits, unhinging prejudices, finding the right motivation for the greater commitment required by the new workflows.
But today my collaborators and all colleagues in the department are the first to look forward to new challenges, because they have verified how organization and standardization translate concretely into involvement and satisfaction for everyone.
Saica Flex Italy: a beautiful story
What is today Saica Flex Italia was founded in Meldola (near Forlì) in 1968 as a family initiative, as a manufacturer of plastic reel bags. By 2016, the year of the transfer of ownership to the Spanish group Saica, it had achieved a very significant turnover and a diverse offer of food packaging printed in flexo and roto, including pouches and vacuum bags, cured meats sachets and pasteurisable and sterilisable flexible packaging.
The company took the Saica Flex name after a leverage buyout operation in partnership with two private equity funds, which accelerated its evolution into a managerial and international company. From then on the company’s story has been one of modernization of plants and the production apparatus, strengthening of the structure, technological and organizational evolution, as well as commercial development in Italy and abroad, favored by the Spanish multinational’s network, size and service capacity.
The group, also of family tradition, operates in 4 main branches of activity in the recovery and recycling of materials and in plastic, and cardboard and corrugated cardboard packaging. The Saica Flex division, the most recent in the group, to which the Meldola hub belongs, employs more than a thousand employees on 8 facilities: in addition to the one in Italy, 2 in Spain, 1 in Luxembourg and 4 in the United Kingdom.
Vision and projects of a forward-looking converter
“A company is made up of people and functions when those who manage it hold a vision, look to the future and know how to renew themselves to face the rapid and continuous changes of our complex modernity”, says Lara Selvi, Plant Manager at Saica Flex who, together with Luca Salatin, has witnessed all the steps from the former Centroplast to what is now the flexible packaging hub of the Saica group. At the Meldola company, this vision is rooted in the sustainability of products and processes, which is nourished by innovation “aimed at developing new types of materials and offering ecological packaging in new areas of application, including non-food, such as stand-alone bags for refilling liquid detergents”.
It is an idea of “integral” sustainability that embraces production processes, resource management, control of waste and discards and, once again, people.
“One of our strengths – emphasizes the manager – has always been our orientation towards the customer and their needs, in order to establish a relationship of trust and collaboration, aimed at true sustainability, an alternative to both green washing and the uninformed demonization of plastic. And networking with our suppliers to keep us up to date with the state of the art.” Saica Flex has many projects, says Lara Selvi. They provide for the development of new films made with recycled materials that fully meet all hygiene and safety standards, the conquest of further space on foreign markets, and investments in new technologies, “for example lamination, to produce laminated products with barrier properties suitable for the most sensitive products and, at the same time, manageable at end-of-life without impacting the environment”.