Eptacromia: la rivoluzione per la stampa rotocalco
Connettività, digitalizzazione, automazione, sostenibilità. Lavorando sui 4 pilastri della vision che guida lo sviluppo del gruppo, Bobst ha messo a punto una nuova generazione di macchine rotocalco. Che raggiunge nuovi livelli di competitività usando meno colori e automazione quanto basta.
Chi parla di roto di solito inizia dicendo flexo. Il confronto è inevitabile: è la tecnologia che conquista quote, è in continua evoluzione, e spesso è anche economicamente vantaggiosa costringendo la rotocalco a rispondere. Contrattaccando sul piano del marketing, per ricordare al mondo quant’è superiore per qualità, per la costanza e affidabilità che tutelano l’immagine stampata del brand, per la maggiore semplicità di gestione, per la possibilità di gestire su un’unica piattaforma quella crescente varietà di processi in linea come accoppiamento e saldanti a freddo, lacche a registro e primer barriera che rappresenta uno dei grandi trend del packaging di oggi… Sul piano commerciale, approcciando con successo nuove nicchie di mercato, che sfruttano al meglio le sue prerogative – tipicamente in ambito security, nella stampa di foil o nel decorativo.
Eptacromia: La Rivoluzione nella Stampa Rotocalco
E soprattutto sul piano tecnologico, dove la roto prepara la riscossa in termini di sostenibilità economica – meno tempi e scarti di avviamento – ed ecologica – largo agli inchiostri all’acqua e ai substrati di nuova generazione – con l’obiettivo ultimo di aiutare i converter ad assecondare le esigenze del mercato.
In Bobst ci si lavora da anni e le macchine di ultima generazione hanno raggiunto livelli di performance che tengono alta la bandiera del gruppo svizzero. Ce ne parlano Jonathan Giubilato, Product Line Manager, e Davide Rossello, Head of Competence Center & Process Manager Gravure, coadiuvati dalla marketer, Sara Alexander. Partendo con un’affermazione forte: «la roto ha bisogno di un cambiamento strutturale, come quello che abbiamo introdotto oltre 20 anni fa con l’albero elettrico e successivamente con la messa a registro automatica. Oggi la svolta si chiama eptacromia. Dopo anni di ricerca e sperimentazione con i partner di filiera, lo scorso settembre siamo stati in grado di presentare dei test di stampa all’altezza delle aspettative, aprendo così le porte dell’ECG alla stampa rotocalco».
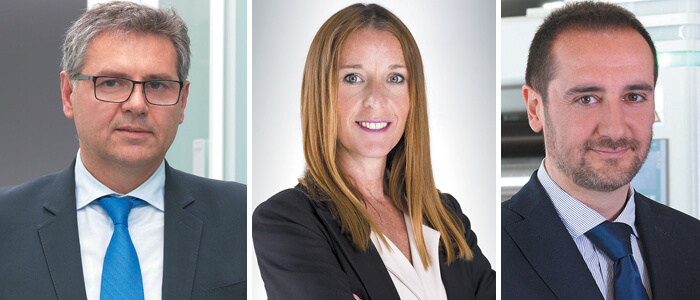
Da sinistra: Jonathan Giubilato, Sara Alexander e Davide Rossello
Dal progetto alla produzione
L’Extended Color Gamut è un metodo per estendere la gamma cromatica dei colori riproducibili in stampa aggiungendo alla quadricromia dei colori base puri (nel caso dell’eptacromia, 4+3) e passando così dalle 3-400mila possibili composizioni cromatiche a circa 750mila.
«La sua adozione limita il numero dei colori utilizzati; evita l’utilizzo di colori spot; riduce drasticamente i tempi di preparazione e i consumi energetici necessari a gestire colori speciali con alta copertura in mezzo alla macchina, permettendo di realizzare macchine con forni più corti e di conseguenza passaggi del nastro più corti, con meno costi. Inoltre questa tecnologia riduce al minimo le parti che devono essere lavate al cambio lavoro (con l’ECG gli inchiostri stanno fissi in macchina) e quindi anche i materiali da smaltire.
Sono vantaggi molto rilevanti, sia economici sia ecologici, che mostrano tutti i loro benefici soprattutto nella stampa di tirature corte dove, per definizione, costi, tempi e scarti di avviamento fanno la differenza».
Fino a poco tempo fa, però, in ambito rotocalco erano vantaggi teorici: per questo in Bobst si celebra il traguardo raggiunto, comprovato non solo dai test delle demo ma anche dalla testimonianza degli utilizzatori che sono passati dalla teoria alla pratica. «La messa a punto di soluzioni ad hoc, soprattutto relativamente alla performance di registro e alla sua gestione semplificata, è stata la chiave di volta e adesso finalmente, dopo la prestampa e l’organizzazione del workflow, anche gli stampatori rotocalco con la macchina Bobst così configurata possono beneficiare di tutti questi vantaggi».
Sviluppi promettenti
Puntando dritto sulla riduzione dei costi e dell’impatto ambientale, la R&D Bobst ha lavorato in simultanea su tutte le funzioni e componenti degli impianti – macchinabilità, controllo di registro, sistemi di asciugamento, ingresso e l’uscita del film, movimentazione dei materiali e dei carrelli – perché tutto concorre al risultato. E, oltre all’ECG, ha portato avanti molti altri progetti di ricerca di ampio respiro, con il coinvolgimento di tutta la filiera.
I più rilevanti riguardano la stampa di quell’insieme composito e in evoluzione continua che sono i substrati plastici alternativi, notoriamente poco prevedibili e difficili da “macchinare”. L’obiettivo era di superare la vecchia idea che “la macchina rotocalco è configurata per una sola tipologia di materiale” e permettere al converter di proporre ai brand owner quelle nuove soluzioni di packaging sostenibile a cui tutti aspirano. «Le principali novità lato macchina hanno interessato la gestione del materiale, il registro e l’asciugamento, e hanno anche aperto la strada alla realizzazione in linea di quelle tipiche applicazioni roto che sono i coating e le laccature, e che in flexo richiedono invece l’impiego complicato e oneroso di tecnologie aggiuntive.
Le sinergie con il know-how di accoppiamento e coating sviluppato a San Giorgio hanno permesso di realizzare nuovi tipi estremamente promettenti di accoppiati sostenibili. E abbiamo molti progetti ancora aperti, con tantissimi partner e riscontri più che incoraggianti».
Connettività e servizio
Nel futuro delle macchine da stampa rotocalco, a dispetto della relativa maturità di questa tecnologia, in Bobst si prospettano dunque parecchi cambiamenti pilotati dall’evoluzione del mercato. Altri, altrettanto o ancor più dirompenti, interessano la connettività delle macchine a monte e a valle della catena produttiva, per raggiungere nuovi livelli di razionalizzazione e di capacità di interazione in ottica 4.0, ma anche, su un altro piano, quel potenziamento dei servizi post vendita che sempre più creano valore e aprono nuovi orizzonti di business.
«Sono tendenze trasversali a tutta la manifattura, che rappresentano una parte rilevante della R&D del gruppo Bobst e producono effetti a cascata, sempre più evidenti, sulla capacità di assistenza da remoto, la manutenzione predittiva e il rapporto uomo-macchina. All’insegna della semplificazione».
[toggle title=”E se la roto base acqua nascesse in Cina?” load=”hide”]Bobst è uno dei costruttori leader di macchine da stampa roto, con un parco installato worldwide di circa 1500 unità e due stabilimenti produttivi rotocalco a San Giorgio Monferrato e Changzhou, mentre il famoso controllo di registro, Registron®, si fa ancora a Losanna.
“In Monferrato”, spiega Sara Alexander, MarCom Flexible Packaging in Bobst, “abbiamo il Competence Center per la roto, l’accoppiamento e la spalmatura per tutto il gruppo, dove sviluppiamo i progetti innovativi, spingiamo l’engineering e l’ibridazione di funzioni, e produciamo le macchine ad alta tecnologia. In Cina, dove l’anno scorso abbiamo raddoppiato le vendite ci siamo attestati come “la Ferrari” della rotocalco, realizziamo modelli che rispondono con le nostre tecnologie migliori alle esigenze più basiche del mercato locale e la cui popolarità si è diffusa in tutto il sud-est asiatico e poi in India, Sudamerica, Africa, Turchia…
Nel sito di Changzhou abbiamo imparato a produrre la qualità richiesta a un prezzo più contenuto, sottraendo complessità e “alleggerendo” gli automatismi delle funzioni che possono essere svolte da manodopera. E soprattutto abbiamo potuto cogliere altre esigenze di quel mercato, ad esempio di sostenibilità: la recente svolta “verde” del Governo centrale cinese ha generato un vivo interesse per l’uso degli inchiostri ad acqua, perché permettono di bypassare l’onerosa gestione dei solventi. Per noi è stato un grande stimolo a sviluppare questa tecnologia nella roto e se ora le nostre macchine sono pronte è anche grazie al gran lavoro fatto nel nostro stabilimento. L’anno scorso l’associazione degli stampatori cinese in rotocalco ci ha insigniti del premio alla sostenibilità per i traguardi raggiunti nella riduzione dei VOC“.[/toggle]