Connectivity, digitalization, automation, sustainability. Working on the 4 pillars of the vision that guides the group’s development, Bobst has developed a new generation of rotogravure machines. That reaches new levels of competitiveness using less color and automation as needed.
Whoever talks about gravure usually starts by saying flexo. The comparison is inevitable: it is the technology that conquers quotas, it is constantly evolving, and often it is also economically advantageous, forcing rotogravure to respond. On the marketing side, to remind the world how superior it is in terms of quality, consistency and reliability that safeguard the printed image of the brand, for the greater simplicity of management, for the possibility of managing the growing variety of in-line processes such as lamination and cold sealing, register lacquers and barrier primers on a single platform, that represent one of the great trends in packaging today… On the commercial side, successfully approaching new niches of value that make the most of its prerogatives – typically in the security field, in foil printing or in decoration.
And, above all, on the technological front, where gravure is preparing to make a comeback in terms of economic sustainability – less start-up time and waste – and ecological sustainability – making way for waterbased inks and new-generation substrates – with the ultimate aim of helping converters to meet market needs.
Bobst has been working on this for years and the latest generation of machines have reached performance levels that hold the Swiss group’s flag high. Jonathan Giubilato, Product Line Manager, and Davide Rossello, Head of Competence Center & Process Manager Gravure, with the help of marketer Sara Alexander, tell us about it. Starting with a strong statement: “gravure needs a structural change, like the one we introduced more than 20 years ago with the electric shaft and then with automatic registration. Today the breakthrough is called heptachrome. After years of research and experimentation with supply chain partners, last September we were able to present print tests that lived up to expectations, thus opening the doors of ECG to gravure printing”.
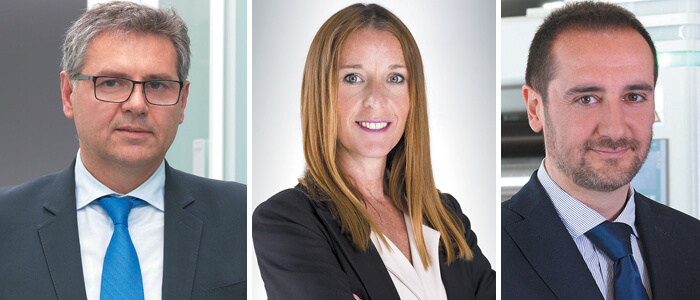
From left to right: Jonathan Giubilato, Sara Alexander and Davide Rossello
From design to production
The Extended Color Gamut is a method for extending the chromatic range of colors that can be reproduced in printing by adding pure basic colors to the four-color process (in the case of 7-color palette, 4+3), thus passing from 3-400 thousand possible chromatic compositions to about 750 thousand.
“Its adoption limits the number of colors used; avoids the use of spot colors; drastically reduces the preparation time and energy consumption necessary to manage special colors with high ink coverage in the middle of the machine, to have shorter dryers and consequently shorter web passages, with less costs. Furthermore, this technology minimizes the parts that need to be washed when changing jobs (with the ECG the inks are fixed in the machine) and consequently the materials to be disposed of.
These are very significant advantages, both economic and ecological, which show all their benefits especially in the printing of short runs where, by definition, costs, times and start-up waste make the difference”.
Until recently, however, in the rotogravure field there were theoretical advantages: this is why Bobst celebrates the milestone reached, proven not only by demo tests but also by the testimony of users who have passed from theory to practice. “The development of ad hoc solutions, especially in relation to register performance and its simplified management, was the keystone and now finally, after prepress and workflow organization, rotogravure printers with the Bobst machine configured in this way, can also benefit from all these advantages”.
Promising developments
Aiming straight at reducing costs and environmental impact, Bobst R&D has worked simultaneously on all plant functions and components – machineability, register control, drying systems, film infeed and outfeed, material handling and trolleys – because every aspect contributes to the final result. And, in addition to the ECG, Bobst has carried out numerous other wide-ranging research projects, involving the entire supply chain.
The most relevant ones concern the printing of the composite and constantly evolving set of alternative plastic substrates, notoriously unpredictable and difficult to “machine”. The aim was to overcome the old idea that “the rotogravure press can be redesigned for one single material type” and allow the converter to propose to brand owners those new sustainable packaging solutions to which everyone aspires. “The main innovations on the machine side have concerned material management, register and drying, and have also opened the way to the in-line production of other typical gravure applications such as coating and lacquering, which in flexo require the complicated and costly use of additional technologies. The synergies with the laminating and coating know-how developed at San Giorgio have made it possible to create new, extremely promising types of sustainable laminates. And we have many projects still open, with lots of partners and have received more than encouraging feedback.”
Connectivity and service
In the future of rotogravure printing presses, in spite of the relative maturity of this technology, at Bobst there will be many changes driven by market evolution. Others, equally or even more disruptive, concern the connectivity of machines upstream and downstream of the production chain, to reach new levels of rationalization and interaction capacity in a 4.0 perspective, but also, on another level, the strengthening of after-sales services that increasingly create value and open up new business horizons.
“These are transversal trends throughout manufacturing, which represent a significant part of the R&D of the Bobst group and produce cascading effects, increasingly evident, on the capacity for remote assistance, predictive maintenance and the man-machine relationship. In the name of simplification”.
[toggle title=”What if waterbased gravure was born in China?” load=”hide”]Bobst is one of the leading manufacturers of gravure printing machines, with a worldwide installed base of about 1500 units and two gravure production plants in San Giorgio Monferrato and Changzhou, whilst the famous register control, Registron®, is still made in Lausanne.
“In the Monferrato,” explains Sara Alexander, MarCom Manager Flexible Packaging at Bobst, “we have the Competence Center for gravure, laminating and coating for the entire group, where we develop innovative projects, push engineering and function hybridization, and produce the high-tech machines. In China, where we doubled our sales last year and have established ourselves as the “Ferrari” of gravure, we make models that respond with our best technologies to the most basic needs of the local market. And from there, their popularity has spread throughout Southeast Asia and then to India, South America, Africa, Turkey… At the Changzhou site we have learned to produce the required quality at a lower price, removing complexity and “lightening” the automation functions that can be carried out by manpower or with simplified means. Above all, we were able to grasp otherneeds of thatmarket, such as sustainability: the recent “green” turnaround of the central Chinese government has generated a keen interest in the use of waterbased inks, because they make it possible to bypass the costly management of solvents. For us it was a great stimulus to develop this technology in gravure printing and if now our machines are ready it is also thanks to the great work done at our site. Last year the Chinese rotogravure association awarded us the sustainability award for our achievements in reducing VOCs “.[/toggle]